前言
水泥行业碳排放结构以直接排放为主,生产制造过程会产生大量的碳排放,存在降碳难度大的问题。海螺水泥是我国水泥行业龙头企业,又是具有国有企业身份,勇于承担推进节能降碳的社会责任,从调整用能结构、创新降碳技术、搭建循环经济、推行低碳管理等方面布局低碳发展,在保持业务增长的同时实现了碳排放强度降低、污染物减排的成效。海螺水泥的低碳发展布局不仅能够为水泥企业的绿色转型提供借鉴,更为降碳难的其他行业生产型企业把握低碳发展痛点、高质量推进碳中和提供经验。
一、海螺水泥低碳布局的必要性
水泥行业具有高耗能高排放的特性,是我国推进碳达峰碳中和目标实现的重点关注领域。截至2020年,水泥行业的碳排放约14亿吨,占全国碳排放的比例达13%(图1),是仅次于电力、钢铁行业的二氧化碳“排气筒”,成为我国推进碳达峰碳中和的抓手之一。2021年11月我国出台了《“十四五”工业绿色发展规划》,对水泥行业低碳发展的目标与举措进行了规划,持续推进水泥行业的节能降碳,水泥行业面临着越来越严格的节能降碳政策。水泥的生产过程为“两磨一烧”,这些环节产生的碳排放以原料分解、燃料消耗产生的直接碳排放为主,通过化学反应直接将温室气体排放至空气中,难以在较短时间内消除,水泥行业存在减碳难度大的问题。因此,水泥行业亟需加速推进低碳发展。
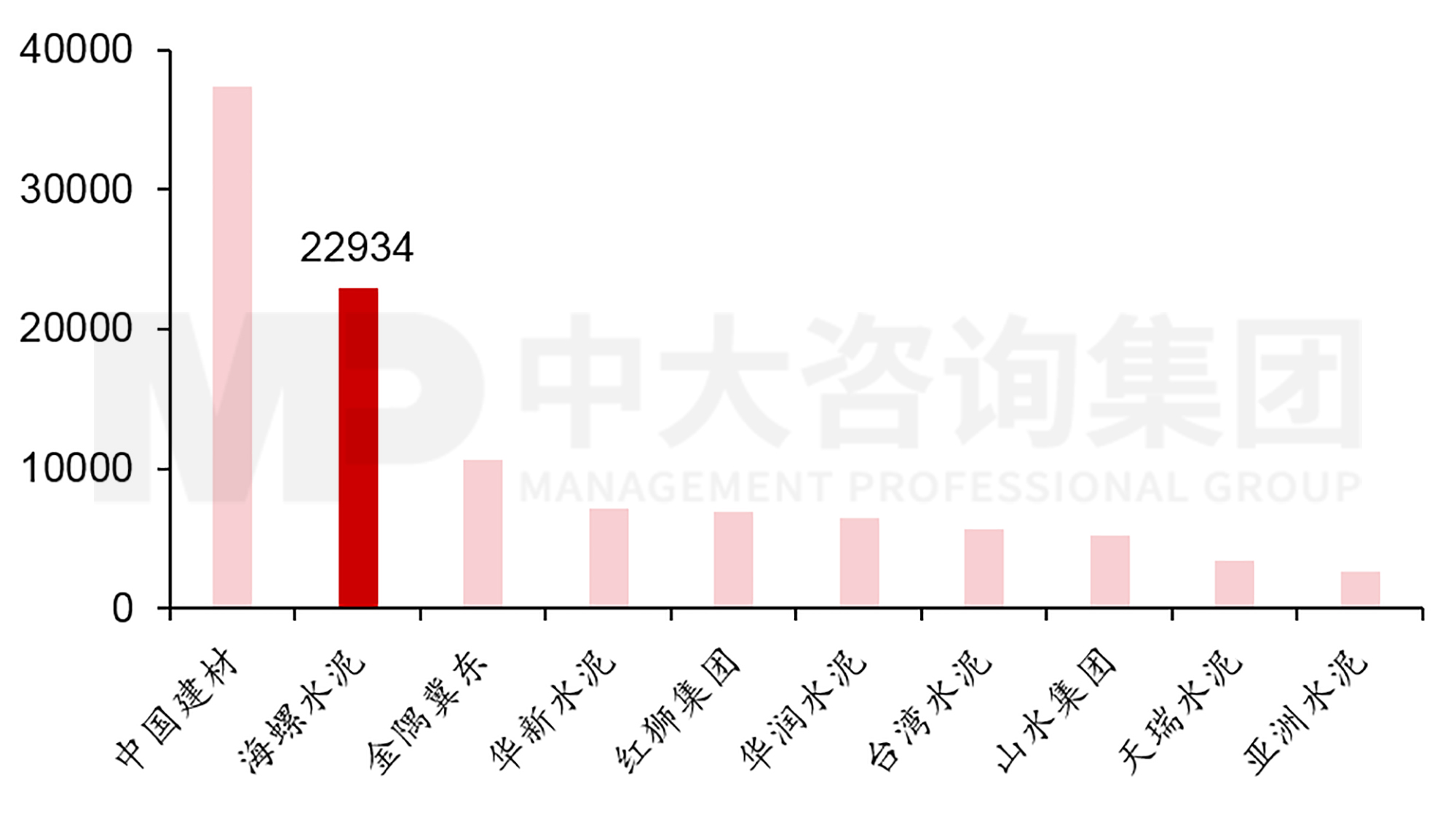
图1 2021年我国水泥行业熟料产能排行
数据来源:中国水泥协会,中大咨询整理
海螺水泥2021年熟料产能位于我国水泥行业中的第二位,是我国水泥行业的头部企业。基于行业转向低碳发展的背景,海螺水泥需要承担推进节能降碳的社会责任,面临低碳发展的外部要求。同时,海螺水泥自身碳排放以范围一下的直接碳排放为主(占比达94%),降低直接碳排放是节能减碳的主要抓手。因此,海螺水泥制定了海螺碳达峰碳中和行动方案和路线图,推进节能环保技术、降碳技术的研发与应用,全面加速海螺水泥的低碳循环发展。
二、海螺水泥低碳发展布局
面对愈发严格的节能降碳政策,海螺水泥以调整能源结构、发展低碳循环、应用降碳技术、推进低碳管理等四条途径实现公司的低碳发展布局。
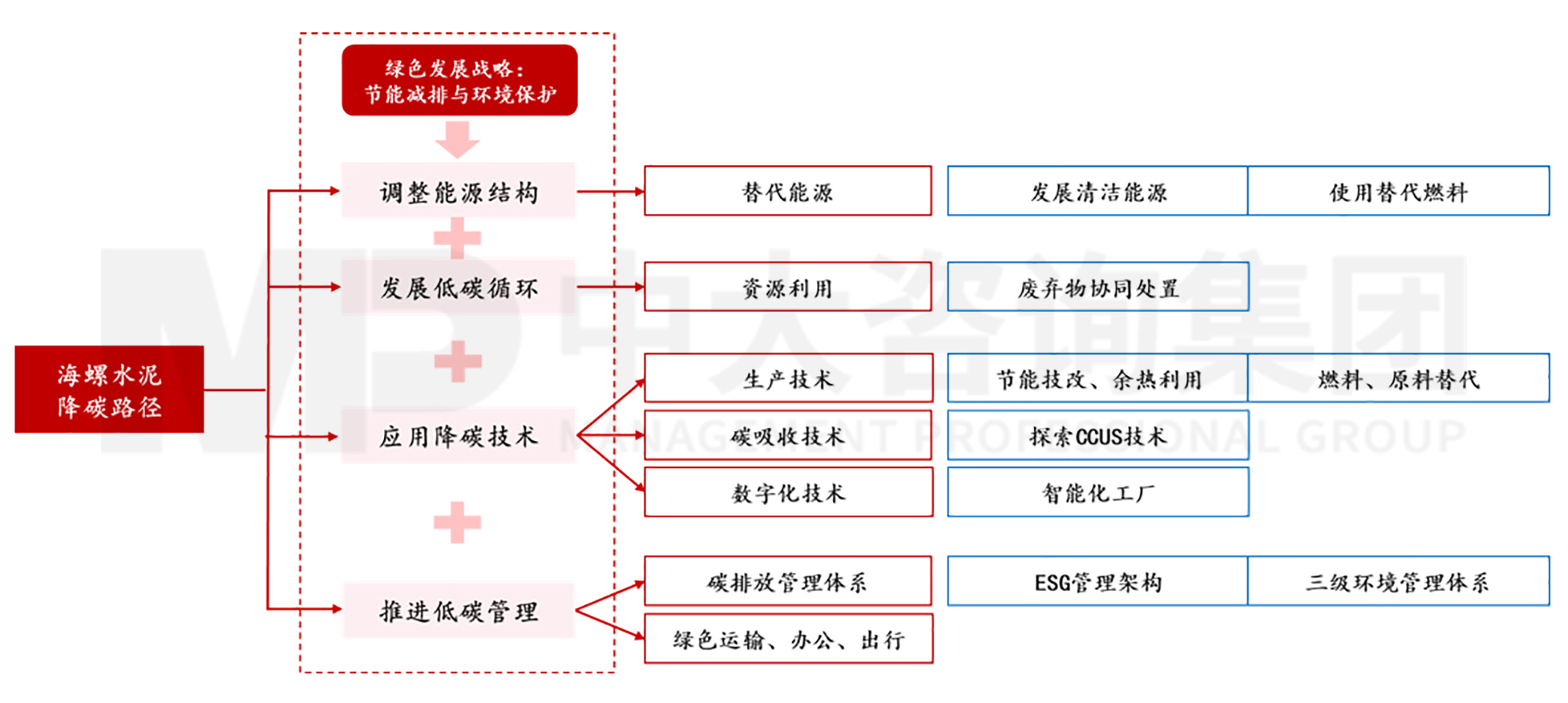
图2 海螺水泥低碳发展布局
数据来源:海螺水泥社会责任报告,中大咨询分析
(一)调整用能结构
水泥生产需要消耗大量的电力,传统水泥厂均采取煤炭发电的方式来提供电力,煤电的使用排放了大量的温室气体。因此,海螺水泥一方面大量投资可再生能源发电,持续提高可再生能源发电对化石能源的替代,如2022年初海螺水泥制定了年投资额达50亿的新能源投资计划,重点推动水泥厂光伏发电、风力发电改造。另一方面,海螺水泥应用替代燃料以减少煤炭等化石能源的消耗,在2020年建成了国内水泥行业首条生物质替代燃料系统,实现生物质燃料替代燃煤率超40%,同时通过阶梯炉、热盘炉等技术的集成应用,将协同处置进行升级改造,使垃圾衍生燃料入窑,进一步提高资源利用率。
海螺水泥在2021年使用了128万kWh的风电、1.64亿kWh的光电、2.2万吨的生物质燃料,分别实现降碳量达741吨、9.53万吨、2.4万吨,新能源替代帮助海螺水泥取得了良好的降碳成效。
(二)构建低碳循环经济体系
海螺水泥以“无害化、减量化、资源化”原则开展废弃物回收再利用与协同处置,减少环境污染的同时节约石灰石资源,推动生产与垃圾处理碳排放降低。在无害化方面,海螺水泥遵循《中华人民共和国固体废物污染环境防治法》的要求,设置危废暂存库,按照危废管理要求定期委托有资质单位规范处置,并做好相应储存、进出库管理,实现水泥生产无害化处理。在减量化与资源化方面,海螺水泥开发水泥窑协同处置城市生活垃圾系统、应用水泥窑利用工业废料技术,实现了水泥窑消化煤矸石、火山灰、脱硫石膏等工业废渣与城市垃圾的功能。
依托于废弃物协同处置与资源再利用技术,海螺水泥实现自身废弃物全部合规处理与再利用,同时还在2021年累计消纳了4366.1万吨的一般工业固体废物、处理生活垃圾93.09万吨、处理危险废物53.02万吨等。海螺水泥在解决工业垃圾的消解问题的同时,减少污染物排放,节约石灰石资源,降低石灰石分解产生的碳排放。
(三)改进降碳技术
1.利用降碳技术降低生产排放
海螺水泥通过节能技改、余热发电、原料替代等方式大幅降低水泥生产过程中直接产生的碳排放。
在节能技改方面,海螺水泥存在电力损耗高、热力利用效率低的问题,其通过改造篦冷机、改造分解炉扩容、使用高效变频风机、使用节能生料辊压机、利用高效低阻旋风筒、使用新型隔热纳米材料等举措推进节能技改。在2021年底完成了10条生产线改造,能够使生产线吨熟料标准煤耗在98千克以内,吨熟料综合电耗在48千瓦时以内,实现节能降碳。
在余热发电方面,海螺水泥面临热力资源大量浪费的痛点,因此其对每个水泥厂添加配套余热发电系统,利用排出的废气余热进行发电,并将产生的电能用于企业生产,减少外购电力。在2021年,集团整体余热发电量达79亿度,减排二氧化碳约459万吨。
在原料替代方面,由于石灰石的主要成分碳酸盐分解过程中产生的二氧化碳约占总排放量的63%,是水泥生产种最主要的碳排放来源,海螺水泥存在石灰石分解产生碳排放的痛点。因此海螺水泥一方面采用黄磷渣配料,降低煅烧温度,减少热力消耗,另一方面选择粉煤灰、硫酸渣、脱硫石膏等工业废料替代部分原料,从而减少碳酸盐分解产生的二氧化碳。截至2021年实现吨熟料煤耗下降1.5kg,同时利用工业废料替代原料减少了石灰石分解直接产生的二氧化碳。
2.创新碳捕集技术提高碳吸收
海螺水泥开展碳捕集利用示范项目,将水泥生产排放的二氧化碳进行资源化利用,既实现碳减排又提高经济效益。海螺水泥在白马山水泥厂建设了全球水泥行业首个水泥窑碳捕集纯化示范项目,实现了对水泥窑尾气中二氧化碳的捕集与资源化利用。
整个系统共分为两步,分别是捕集与利用。第一步中,首先捕集提浓,使水泥窑尾气通过脱硫水洗塔、吸收塔、换热器、解吸塔等设备,实现CO2捕集与提纯;其次压缩分水,将捕集后提纯的CO2经过冷却机、压缩机、脱硫床、干燥床,进行气体的冷却压缩,并分离气体中的水分,再次进行纯化;最后纯化液化与精馏,将脱水后的高浓度气态CO2通过吸附床、液化系统进行纯化液化,随后通过精馏塔进行精馏,形成工业级与食品级CO2。第二步主要是二氧化碳的利用,将制成的CO2进行封存与运输,之后将CO2通过保护焊接、碳酸饮料添加、食品保鲜、干冰生产、电子医药应用等方式进行资源化利用。
目前海螺水泥白马厂碳捕集项目每年可生产3万吨食品级和2万吨工业级CO2,为从吸收端降低水泥生产中排放的二氧化碳量进行了有益的探索。
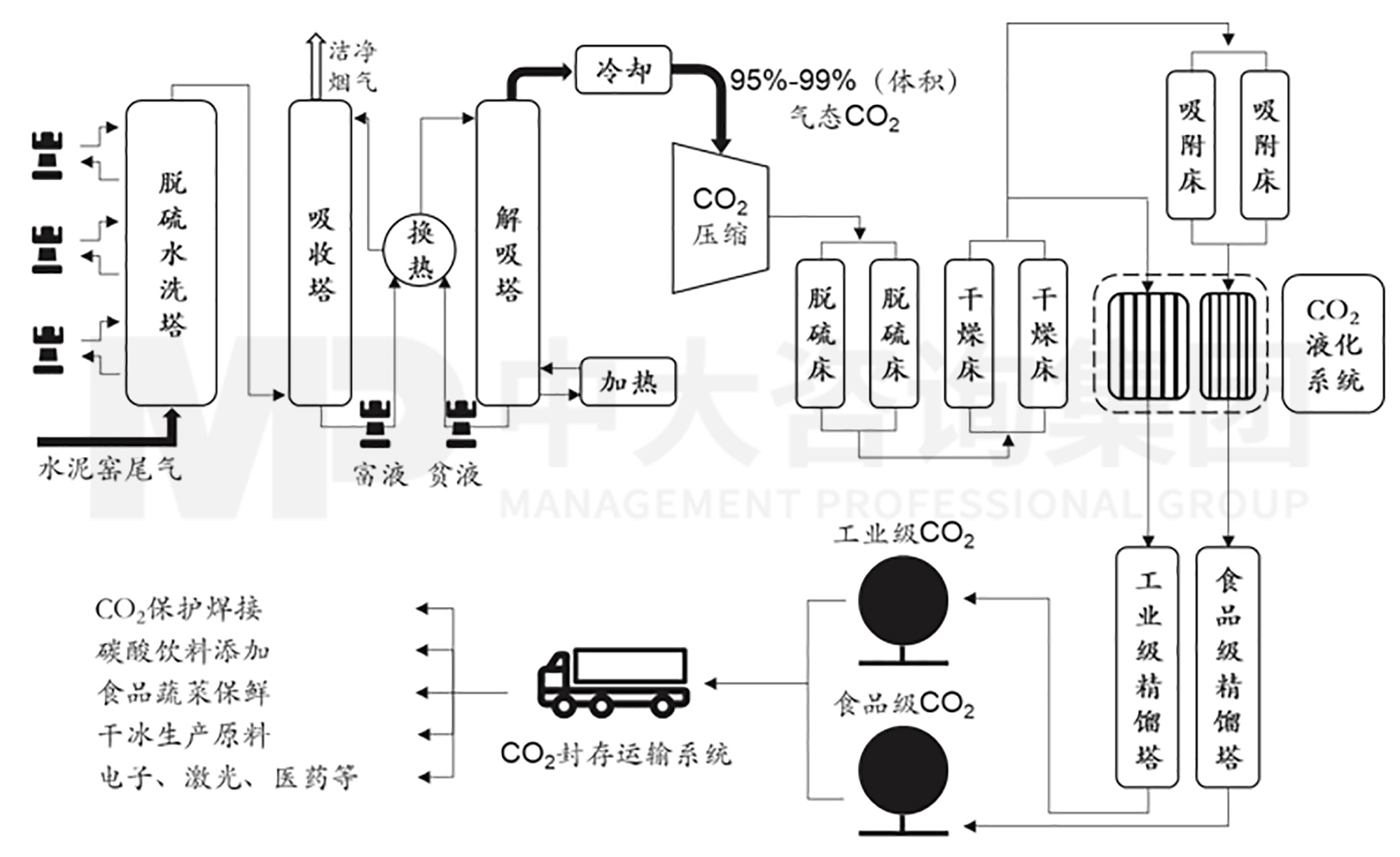
图3 海螺水泥白马山碳捕集项目技术流程
数据来源:海螺水泥集团,中大咨询整理
3.应用数字化技术优化能源管理
对于矿山开采,海螺水泥搭建了数字化矿山系统来推进节能降碳。海螺水泥已投入2亿元推进数字化建设,目前建设了24家数字化矿山。数字化矿山系统依托于数字采矿平台、生产执行平台、三维可视化平台等三大平台,搭建了矿山采掘各单元的智能调度与监控系统,对矿山资源、开采环境进行实时监控,实现矿山勘探、原料开采、矿物运输的集中管理,利用智能化分析优化矿山开采过程,提高采矿效率、降低采矿能耗,减少采矿碳排放。
对于工厂生产,海螺水泥搭建智能生产平台、运维管理平台、智慧管理平台等,开展工厂生产全流程智能管理,依托平台形成了以智能生产为核心、以运行维护做保障、以智慧管理促经营的智能生产模式,打造智能工厂。基于智能化工厂,海螺水泥推进全流程能耗管控,探索高耗能、高排放环节,利用智能分析工具持续优化水泥生产煤电能耗情况,从而减少生产中的碳排放。
(四)践行低碳管理
1.构建三级环境管理体系
海螺水泥为推进低碳发展战略的落实,建立了自上而下的环保管理体系,以总部—区域—子公司三级环境管理架构推进节能环保工作。总部级别的环境管理部门负责统筹集团的节能降碳目标、制定节能降碳工作计划、组织节能减排专业培训,并对子公司进行监督排查。区域级环境管理部门负责落实总部制定的节能减排中长期发展战略,并统筹管理各区域的节能减碳工作,负责把控区域节能减排情况,并对总部进行汇报。子公司环境管理部门需要按照总部要求来实施环保管理措施,推进节能减碳目标的实现。
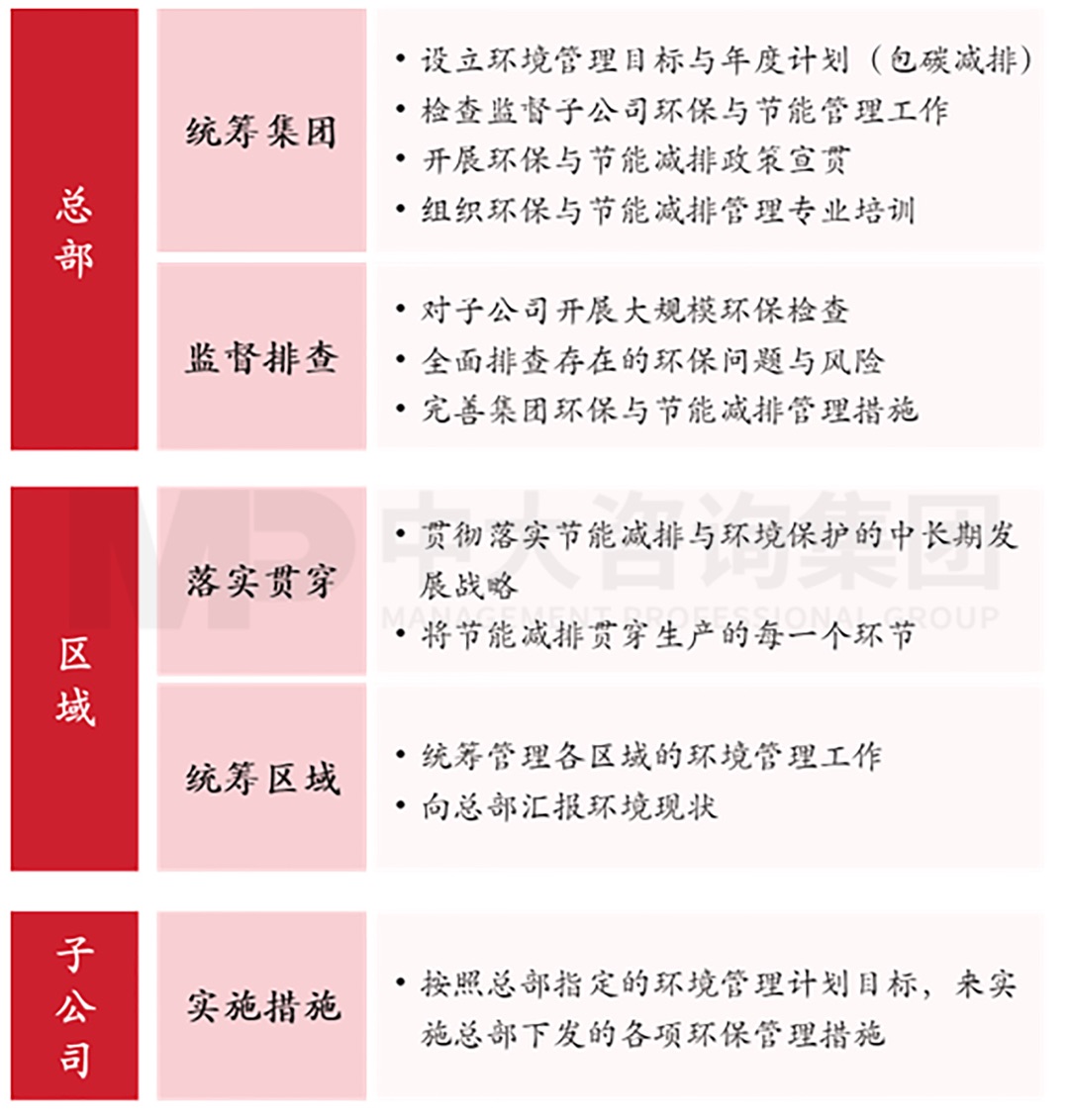
图 4 海螺水泥三级环境管理体系
数据来源:海螺水泥社会责任报告,中大咨询整理
2.建设低碳文化
海螺水泥针对不同的降碳场景采取相应的举措来推进员工参与减碳。首先,海螺水泥通过低碳文化宣传帮助员工树立低碳意识,利用集团内网、微信群、海报等宣传方式,持续加大低碳环保理念宣传力度。其次,通过无纸化办公、应用节能灯具和定制空调等措施培养员工在工作中的低碳办公习惯,降低集团商务楼宇办公产生的碳排放。最后,鼓励员工低碳出行,海螺水泥要求员工合理安排商务活动,减少不必要的出行,鼓励日常商务出行优先选择乘坐公共交通,同时提高视频或者电话会议开展商务洽谈的比例。
(五)低碳发展成效明显
海螺水泥业务增长与碳排放逐步脱钩,且碳强度、单位熟料碳排放、污染物排放持续下降,低碳发展取得良好成效。在碳排放方面,海螺水泥虽然碳排放仍在增长,但是营业收入在5年间复合增长率达17%,而碳排放增长率仅为1.6%,营业收入的增长已与碳排放逐步脱钩,而且降碳技术的应用使单位熟料碳排放、碳强度逐年下降,海螺水泥的低碳发展取得了良好的效果。在污染物排放方面,除2018年氮氧化物略有上升之外,海螺水泥的氮氧化物、二氧化硫、主要排放口颗粒物排放量逐年下降,水泥生产造成的环境污染水平逐年降低。
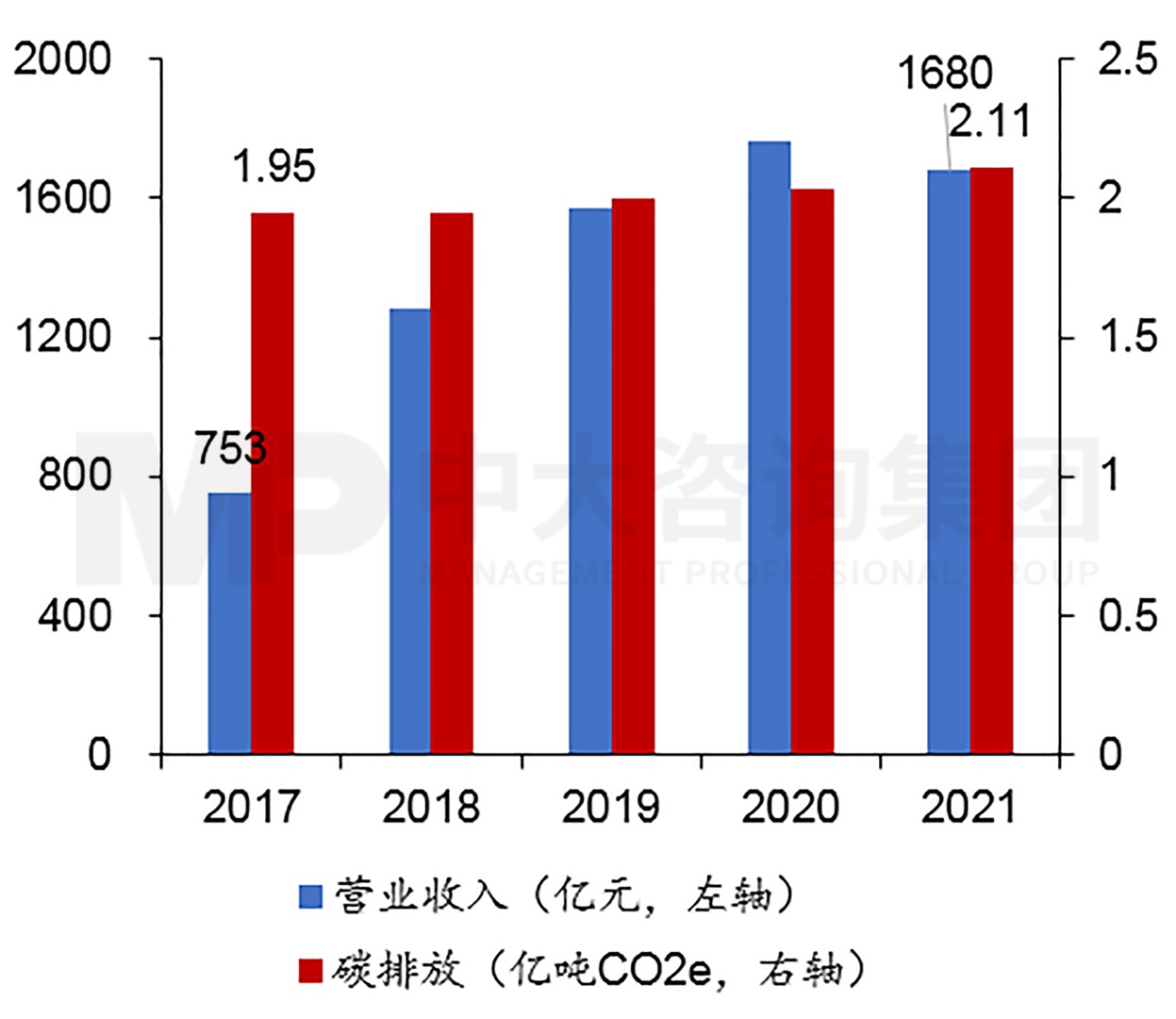
图5 2017-2021年海螺水泥营业收入与碳排放
数据来源:海螺水泥年报与社会责任报告,中大咨询整理
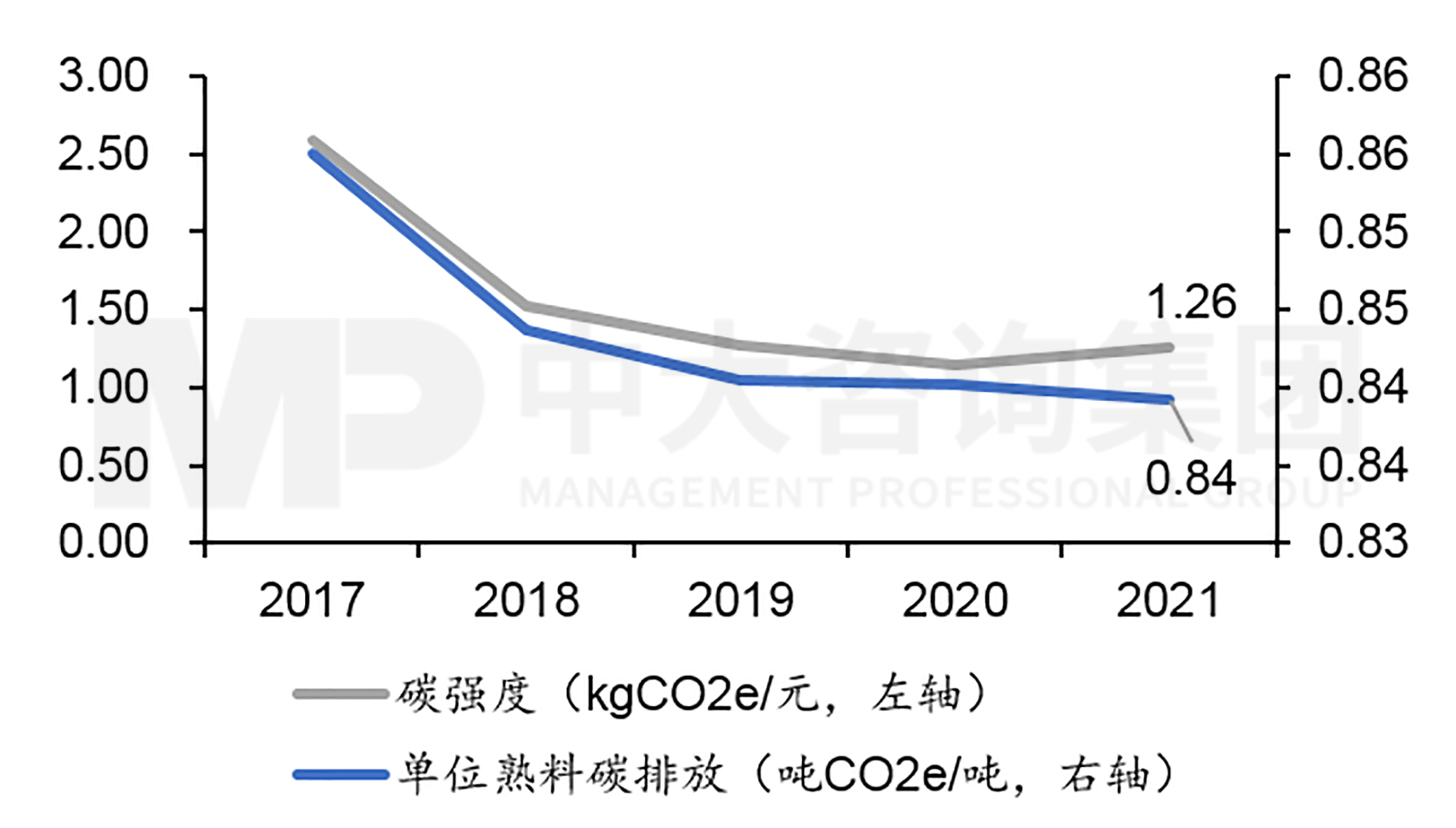
图6 2017-2021年海螺水泥碳强度与单位熟料碳排放
数据来源:海螺水泥年报与社会责任报告,中大咨询整理
在污染物排放方面,除2018年氮氧化物略有上升之外,海螺水泥的氮氧化物、二氧化硫、主要排放口颗粒物排放量逐年下降,水泥生产造成的环境污染水平逐年降低。
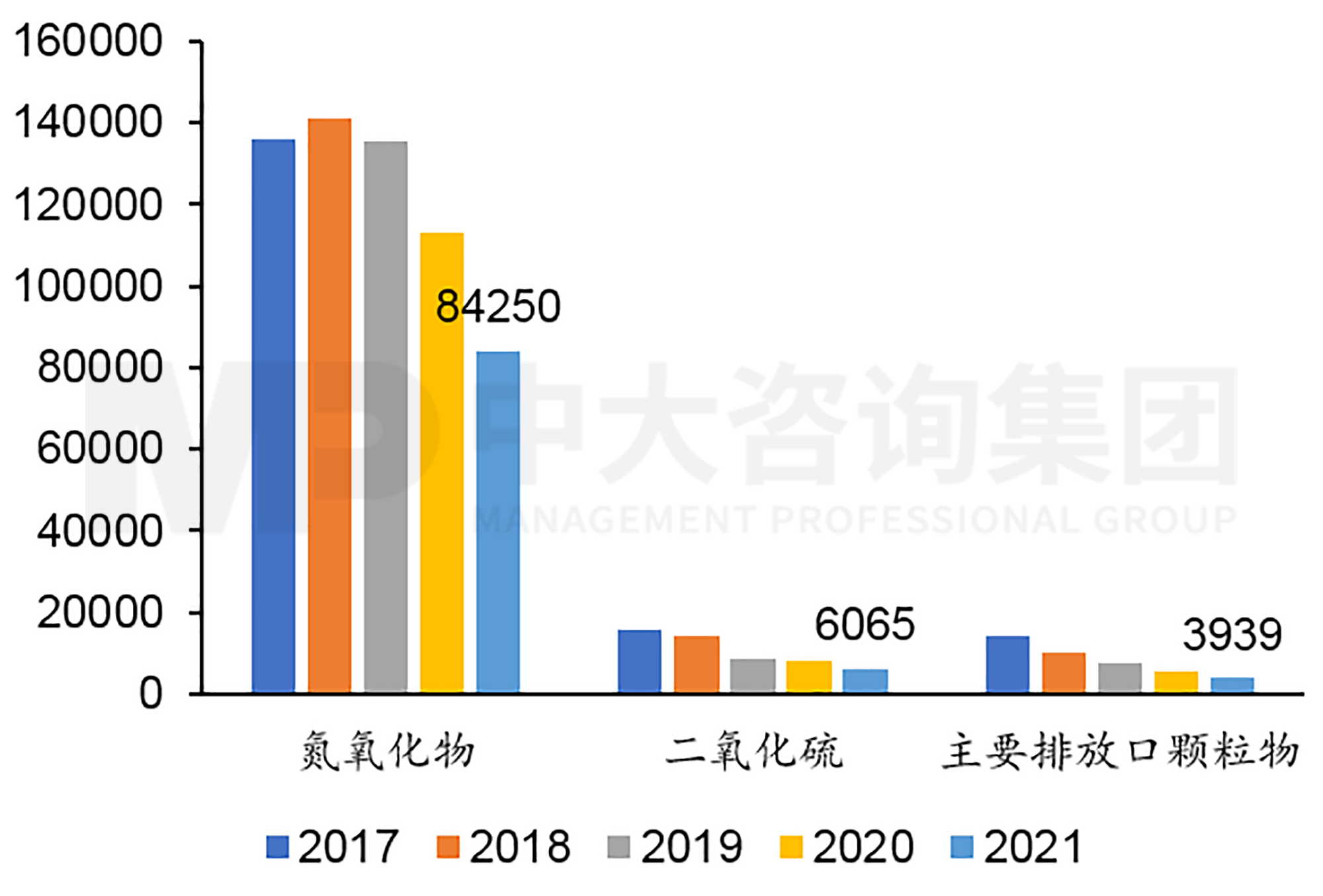
图7 2017-2021年海螺水泥污染物排放
数据来源:海螺水泥社会责任报告,中大咨询整理
三、海螺水泥低碳布局启示
海螺水泥重点从用能结构、低碳循环、技术创新、低碳管理等途径推进公司的节能降碳,力图解决水泥行业降碳难度大的问题。海螺水泥的举措同样为降碳难的其他行业生产型企业把握低碳发展痛点提供了经验借鉴,从调整能源结构、加强技术创新、完善管理体系等方面推进节能减碳,完成低碳发展布局。
(一)调整能源使用结构
水泥等高碳排放产品在生产过程中消耗了大量的化石能源与电力能源来供热供电,产生了大量碳排放。因此高排放的生产型企业可以在工厂内建设光伏发电、风力发电站,充分利用可再生资源,提高可再生能源在能源消耗中的使用比例。同时,搭建智能储能系统,对可再生能源发电进行调峰,还能将多余的电力并网卖出,实现节能降碳并提高收益。此外,还可以建设生物质能源燃料替代系统,通过应用生物质能源提高碳利用效率,从而推进生产过程中的节能降碳。
(二)推动减碳技术创新
以直接排放为主的水泥等产品的碳排放主要来源是生产过程中的化学反应以及煤炭发电,因此高排放的生产型企业需要从搭建资源循环体系、推动生产节能技改、应用数字化技术、研发碳吸收技术等方面开展技术创新,推进企业低碳发展。
在资源循环体系创新方面,依托于生产技术改进,生产型企业需要在保证产品质量的基础上实现对工业垃圾等废弃物的消纳,对废弃物资源循环利用的同时减少产品原料的使用,降低产品生产过程中的直接碳排放。
在生产技术创新方面,应用节能技改、余热发电、原料替代、燃料替代等技术,提高能源与原材料的利用效率,降低碳强度与单位产品碳排放,实现企业的节能降碳。
在碳吸收技术创新方面,高排放的生产型企业可以联合科研院所、行业领先企业建立联合实验室,推进碳捕集封存及利用技术的创新,提高二氧化碳吸收与利用的能力,为实现企业碳中和奠定技术基础。
在数字化技术创新方面,依托数字化平台搭建原料开采、产品生产智能管控系统,实现智能化矿山与智能化工厂,对企业能耗进行控制,制定企业能耗优化方法,推进节能降碳。
(三)完善低碳管理体系
完善的环境治理体系是降碳技术能够有效推进的保障,高排放的生产型企业可以搭建ESG治理架构,形成ESG治理机制。同时在ESG治理下的环境管理方面依托ISO140001环境管理体系认证,建立多级环境管理体系,持续推进节能降碳工作。
低碳文化的构建有助于帮助员工养成节能降碳的习惯,不仅帮助企业降低成本、贯彻节能理念,更能帮助企业降低范围三内的碳排放。因此,水泥企业可以通过理念宣贯、员工培训的方式来培养员工的习惯,形成企业整体的绿色低碳文化。